Students learn to create a range of effects by hacking outdoor kilns built at the nearby nonprofit arts center.
Advanced RISD Ceramics Studio Adapts Mass Production Techniques for Artistic Invention
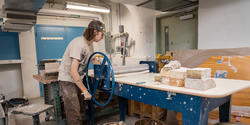
Students in a fall Ceramics studio are exploring various industry techniques developed to enable mass production, including molding, casting, RAM pressing, extruding and wheel throwing. Led by Associate Professor Shoji Satake, the course encourages students to adapt these methods of making as a form of individual artistic expression.
“Understanding how production processes can be used to create multiples is important,” Satake says, “and some of the equipment involved gives artists more options. For example, you can use the RAM press to create work in any shape you want. The potter’s wheel limits you to round pieces.”
Students in the class are working in groups to create batches of mosaic tiles using the RAM press, a mechanical hydraulic machine, and dies (or molds). They begin by collaborating on a design and then create the dies (top and bottom to shape the front and back of each tile) by pouring plaster into cast iron casings. Once the dried and cured dies are set into the press, a slab of clay is placed between them. By pulling down on the lever, they can quickly knock out multiple tiles with absolute consistency from piece to piece.
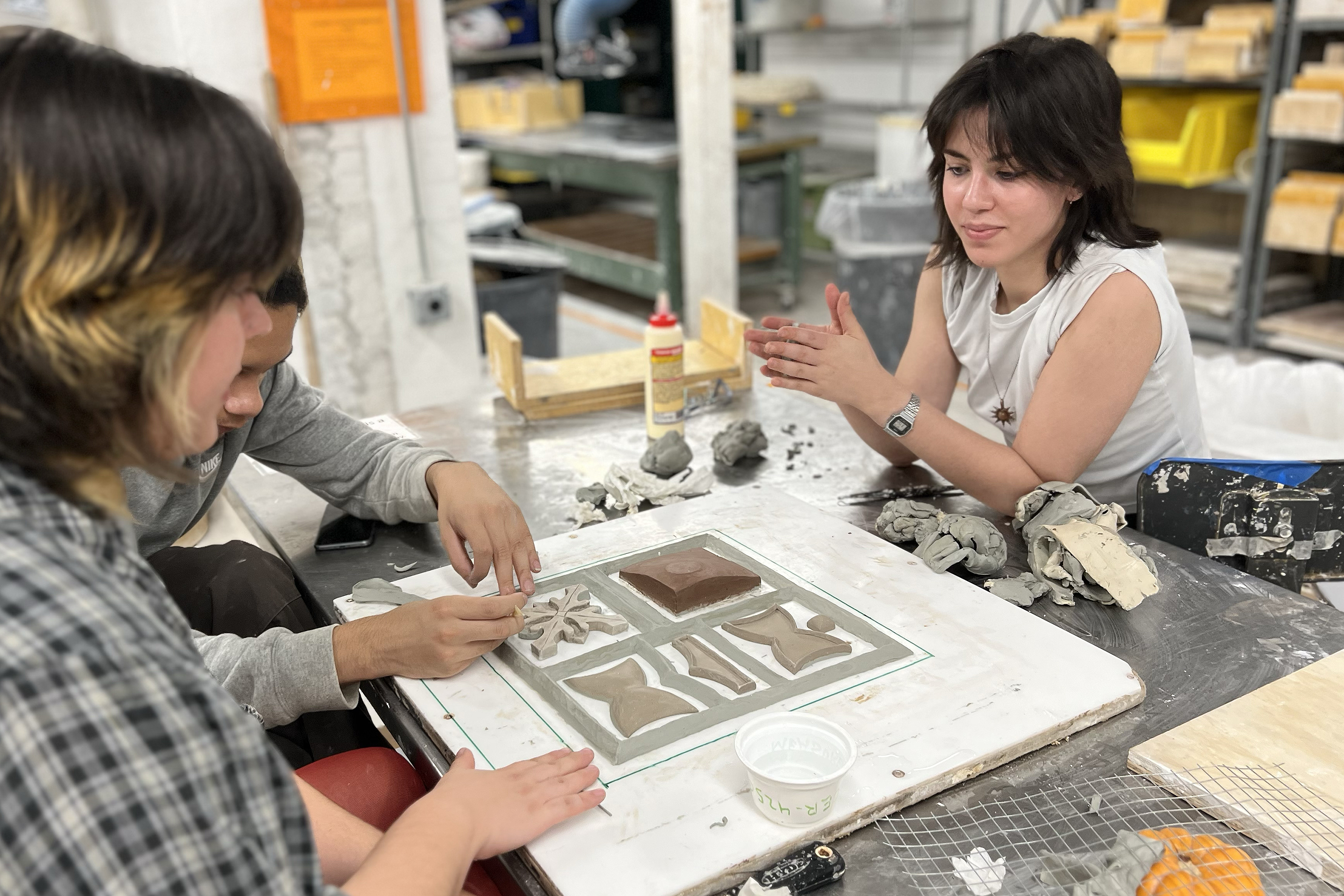
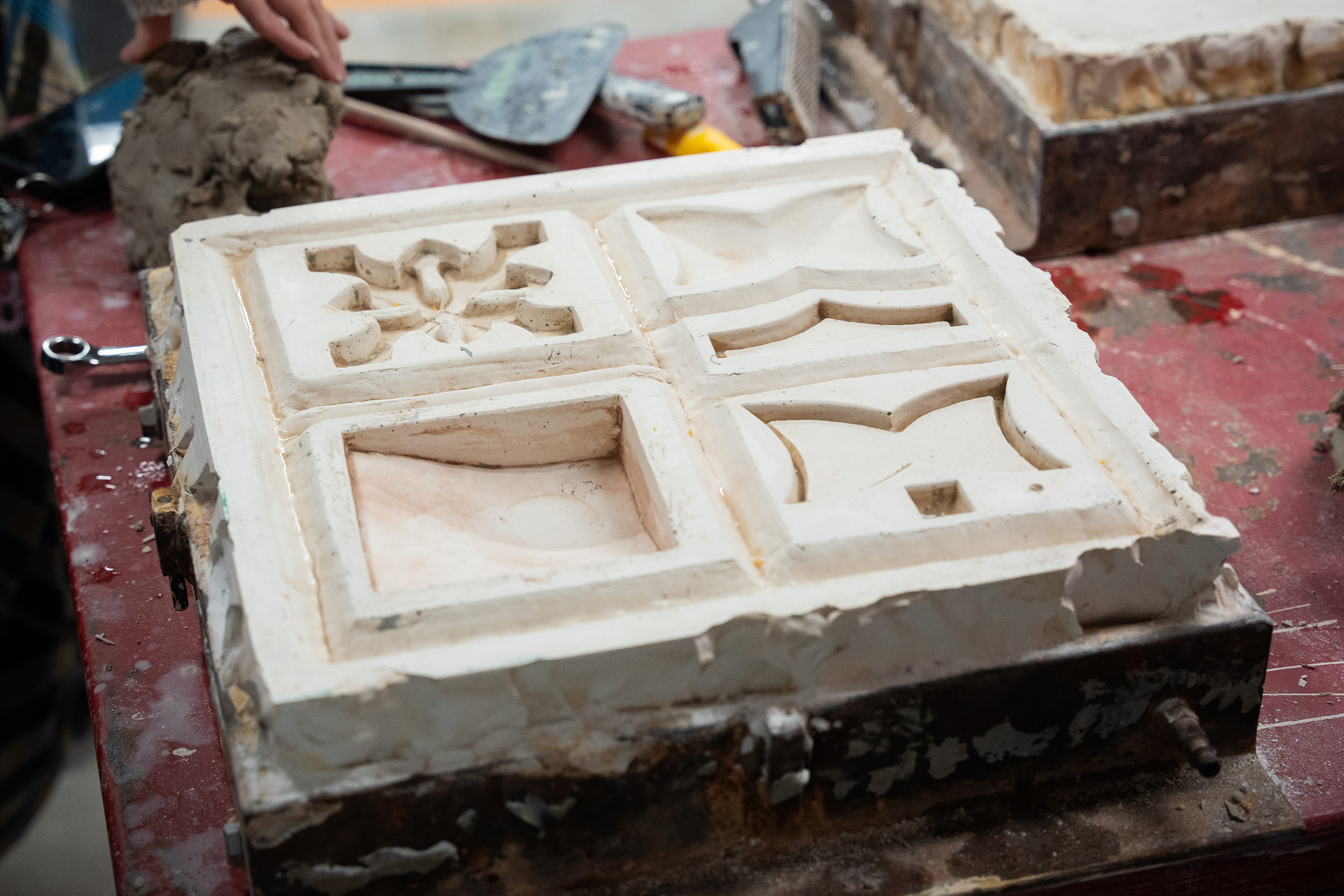
“You could realistically make 300–400 tiles (or whatever objects you’re making) in one day,” says Satake. “It’s a smart, efficient tool that has been around for about 80 years.”
There is one caveat, though: the presses are extremely finicky, and a lot of time can be spent troubleshooting. “We run into a lot of issues with the machinery,” says senior Lewis Shaw 25 CR (see top photo), as he helps Satake figure out which air hose is malfunctioning. “One thing that has been surprising is just how labor-intensive it is to make a die. It’s one thing to hear about it and another to experience it yourself!”
One of the issues is the consistency of the clay, Satake explains. “Moisture needs time to soak into the clay in order to create a membrane between the clay and the die.”
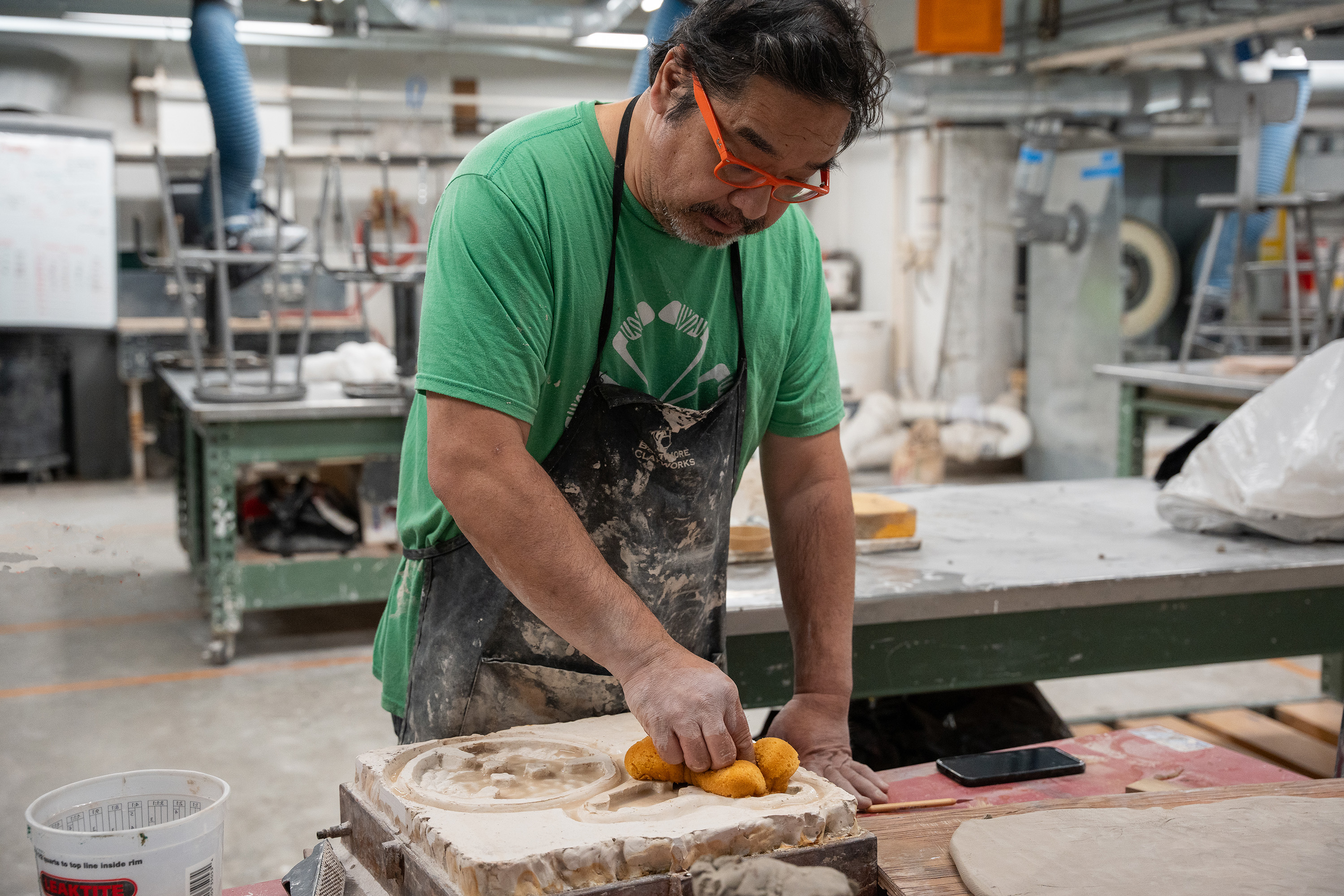
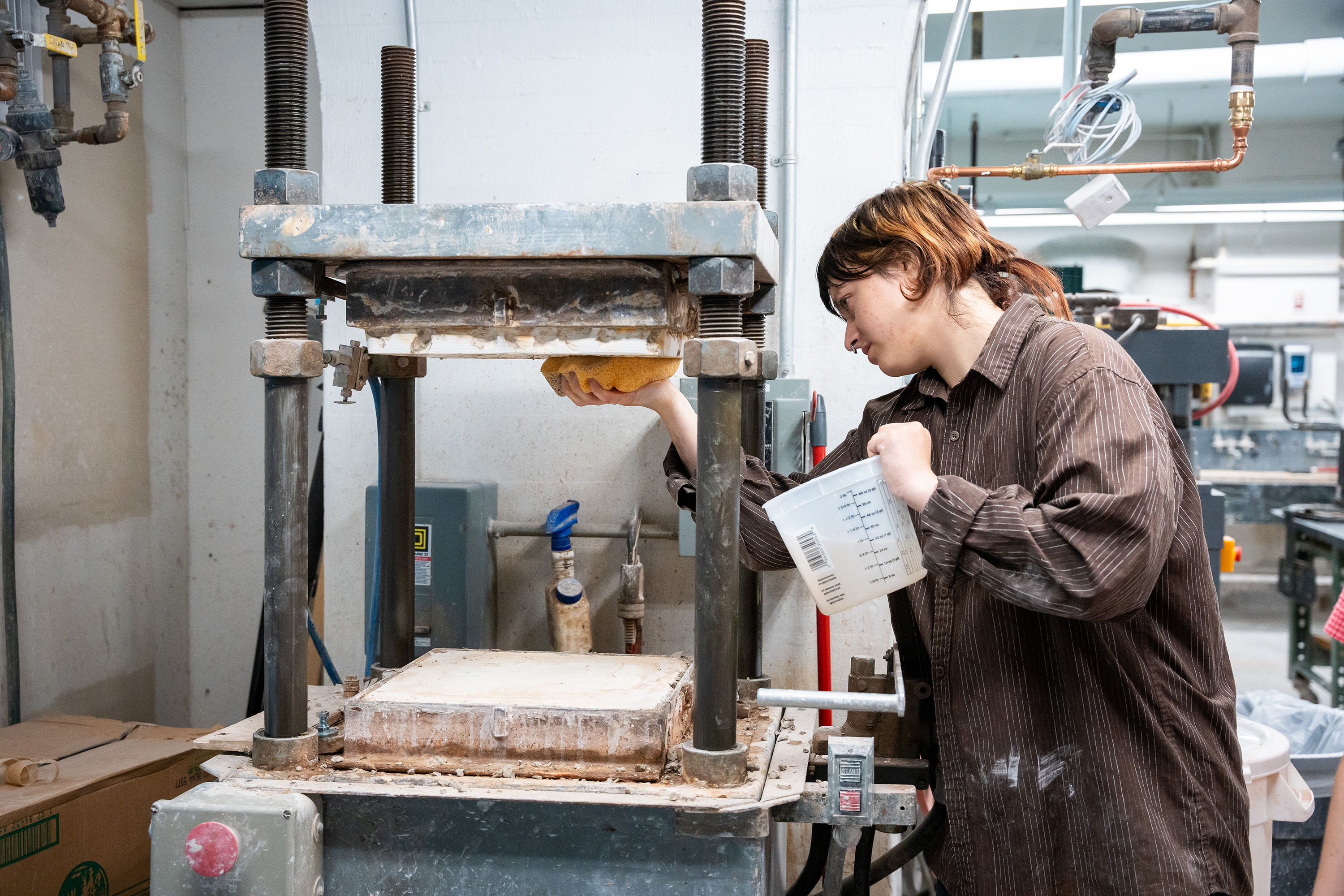
Senior Julia Ambros 25 CR begins to roll out clay slabs for the class to use the following day. “Clay is hard to wrangle when it’s dry,” she says, “so I’m prepping these in advance so they’ll have time to dry.” It’s also important to center the clay between the dies, leaving space around the edges for any excess clay that is squeezed out during the pressing.
Once the group assignment is completed, students will turn to individual, self-directed projects focusing on the same mass-production techniques. Satake requires each of them to dedicate a sketchbook to the class, which they can also use to collect images and other sources of inspiration and generate ideas for their final creations.
Simone Solondz / photos by Kaylee Pugliese
December 2, 2024