A multidisciplinary Wintersession class co-taught by faculty members Anais Missakian and Pete Oyler is focused on curating, producing and executing every aspect of the exhibit.
RISD’s Ceramics Department Fires Up New Raku Kiln at the Steel Yard
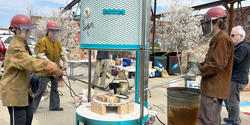
One of the great things about studying Ceramics at RISD is becoming part of the close-knit community of local ceramists not only on campus but throughout the city of Providence and beyond. The department has partnered with artists and educators at the Steel Yard, a nonprofit arts center on the city’s west side, for decades and continues to benefit from the site’s large outdoor space on a regular basis.
“I was the studio manager and a teacher at the Steel Yard before coming to work at RISD,” says alum and faculty member Jane Dillon 79 CR/MA 12, “and the folks who work there, including Howie [Sneider 02 SC, executive director], are always welcoming. They just keep moving forward and working to improve the Woonasquatucket Watershed and the Valley Arts District.”
Dillon and a group of sophomores in her spring pottery studio are part of a large contingent of RISD ceramists who have migrated to the Steel Yard for a day of making. The sun is shining and music blares from an old-school boom-box as Department Head Katy Schimert, Associate Professor Lesley Baker MFA 00 CR and studio tech Nicholas Oh MFA 18 CR fire up three kilns at the site: a massive soda kiln Oh and late RISD Professor Larry Bush built together, a smaller luster kiln and the department’s brand-new raku kiln.
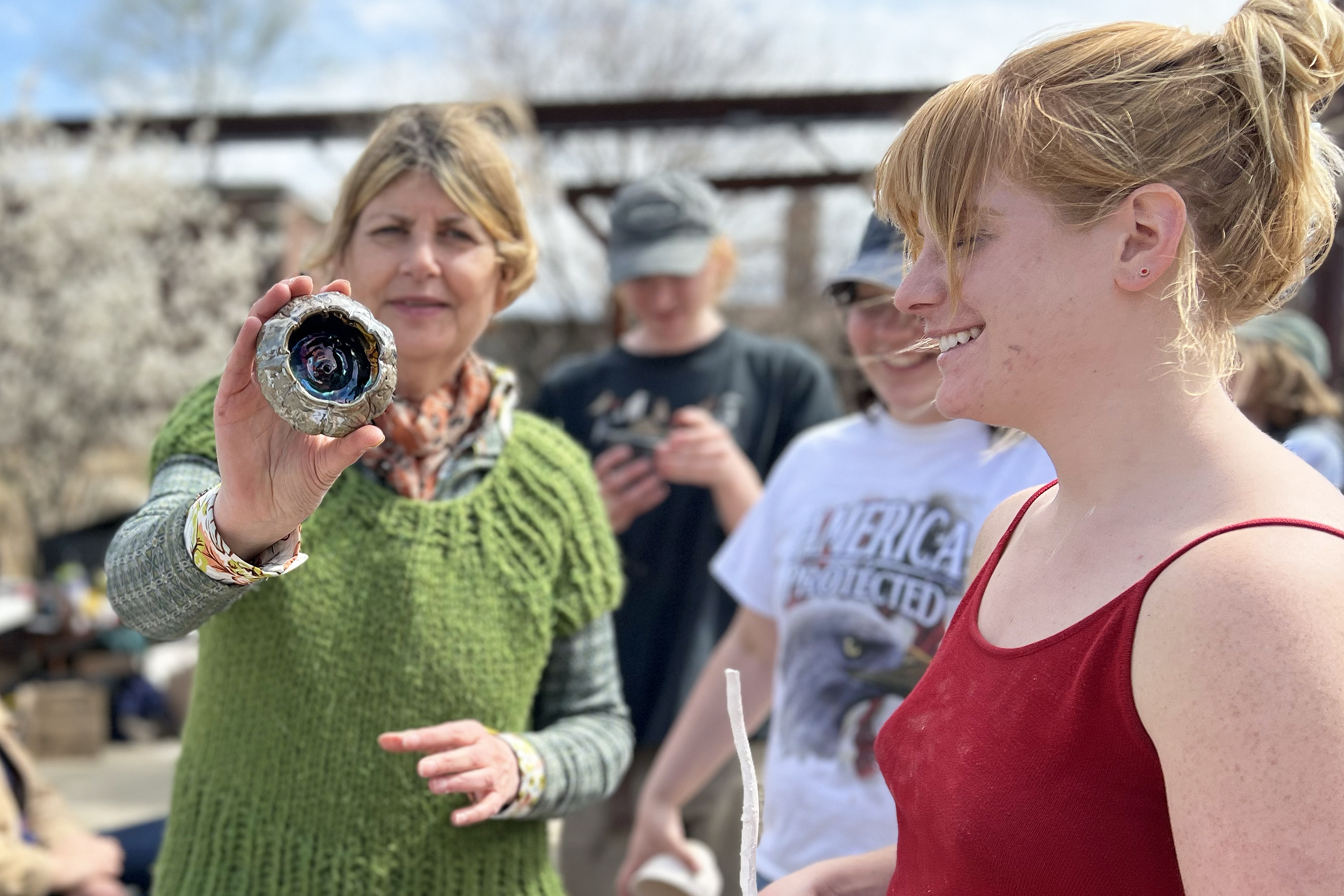
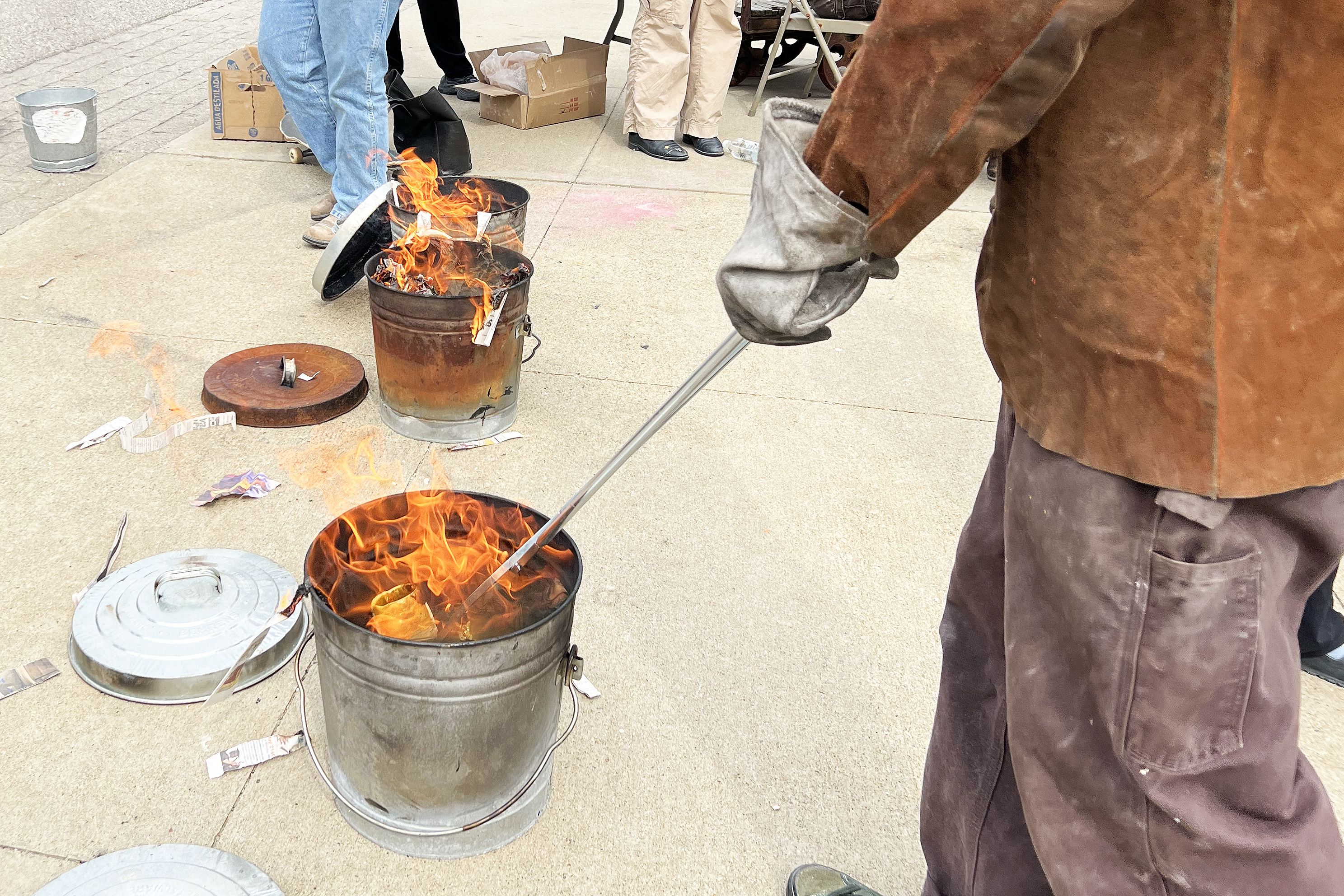
“It’s the maiden voyage of our fancy new raku kiln!” Schimert exclaims. “You get these different kinds of metallics you can’t get with other kilns,” she adds, holding up a small, shiny bowl that has already been fired.
Raku-style pottery was invented in Japan in order to create ceremonial tea ware and is known for its low-temperature fire range. Dillon and Baker are constantly checking the pyrometer they’re using to track the temperature as students suit up in protective gear and get ready to remove the fired pieces. The oxygen-starved atmosphere inside the kiln reacts with the glazes that have been applied, turning copper carbonate, for example, into a rainbow of colors. When the pieces are hot enough, they will be transferred to metal bins filled with combustible materials like paper and wood shavings, which will blacken the clay and shine up the glaze. “We’re looking for a temperature of 1700 degrees Fahrenheit,” Baker notes.
At the back of the yard, grad students Katharine Frank MFA 25 CR and Ana Popescu MFA 25 CR are working with Oh to methodically raise and lower the temperature of the luster kiln, a low-temperature firing technique that originated in the Middle East to create ceramics that were as luxurious as the high-temperature porcelain plateware arriving from Asia on the silk road. “The first round gives you iridescent blues, purples and silvers then metallic greens and coppers and finally golds,” Popescu explains.
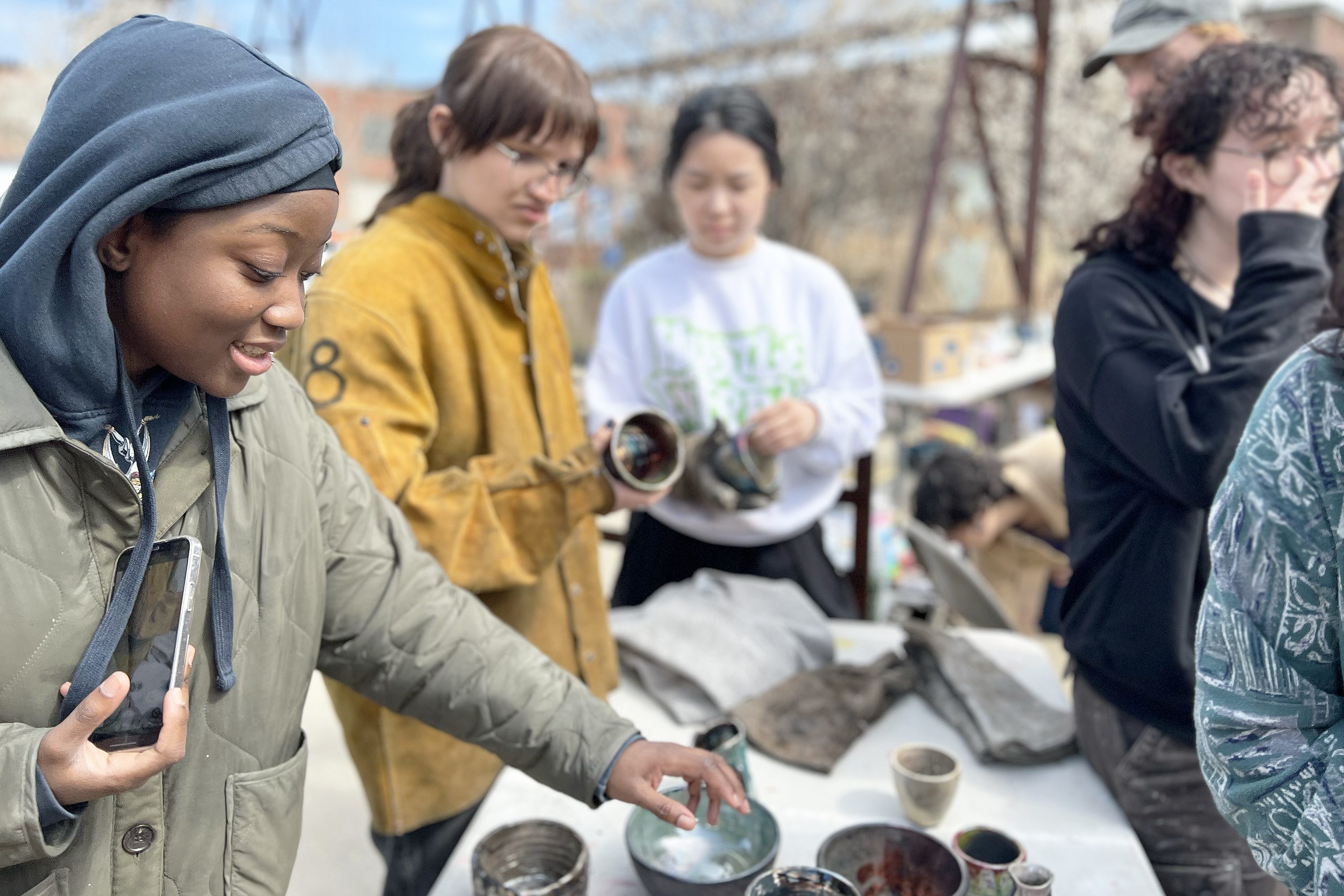
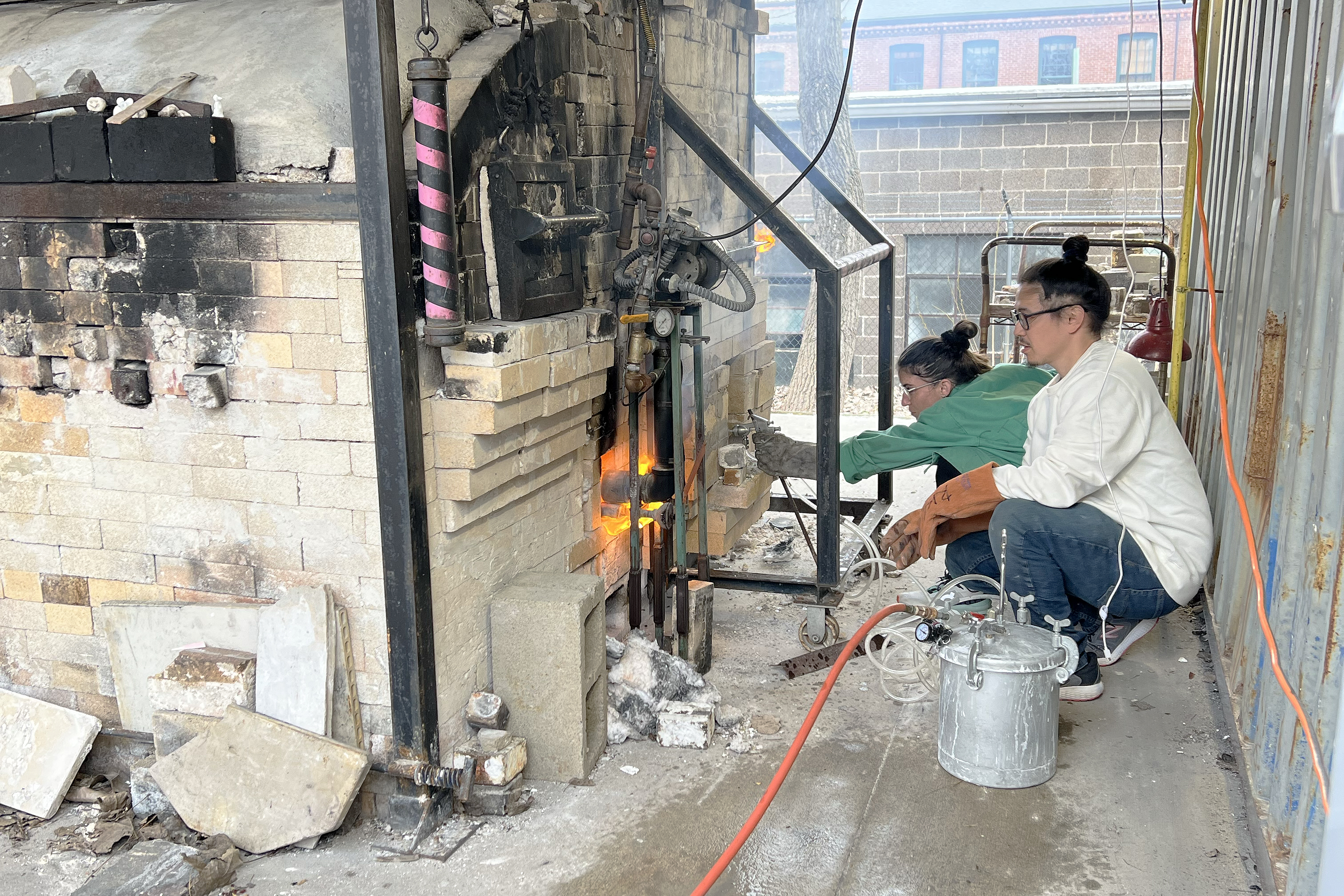
Schimert says she first learned the technique a decade ago from Iranian student Hosseinali Saheb Ekhtiari MFA 13 CR. “International students bring different techniques and technologies from different areas of the world,” she says. “It’s so important for current students to understand how important the atmosphere inside of each kiln is and to get hands-on experience hacking these outdoor kilns to create different effects.”
Oh calls out to the group from the soda kiln, where he has prepared a tank of bicarbonate of soda to be sprayed onto the ceramics midfire. It will bond with the silica in the clay and create a glossy glaze with iridescent flashing. Schimert reminds a student reaching out for the equipment to secure her goggles and apron first. “Ceramics is so much about community,” she says. “You really have to work together.”
Simone Solondz
June 12, 2024