A devotee of historical workwear, the environmentally conscious new grad will show his all-cotton collection at New York Fashion Week in September.
RISD Students Design and Build Bespoke Cowboy Boots in Wildly Popular Studio
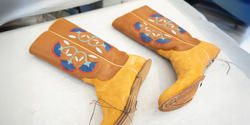
“I love cowboy boots so much,” says grad student Zorka Zsembery MArch 27. “One of the coolest things about studying at RISD is that you can be an Architecture major and learn how to make boots!”
Zsembery is one of 12 RISD students enrolled in The Cowboy Boot, a popular new Wintersession course that straddles the Apparel Design and Industrial Design departments. “It’s a traditional art form that isn’t typically taught in a school setting,” says course instructor Sarah Guerin BArch 99, who also studied Architecture when she was a student at RISD.
“The North American cowboy boot is an iconic symbol of cultural individualism that bridges design, making, function and fashion,” Guerin adds. “The boot itself is at heart a functional object: a work tool whose construction techniques have remained unchanged since the late 1800s.”
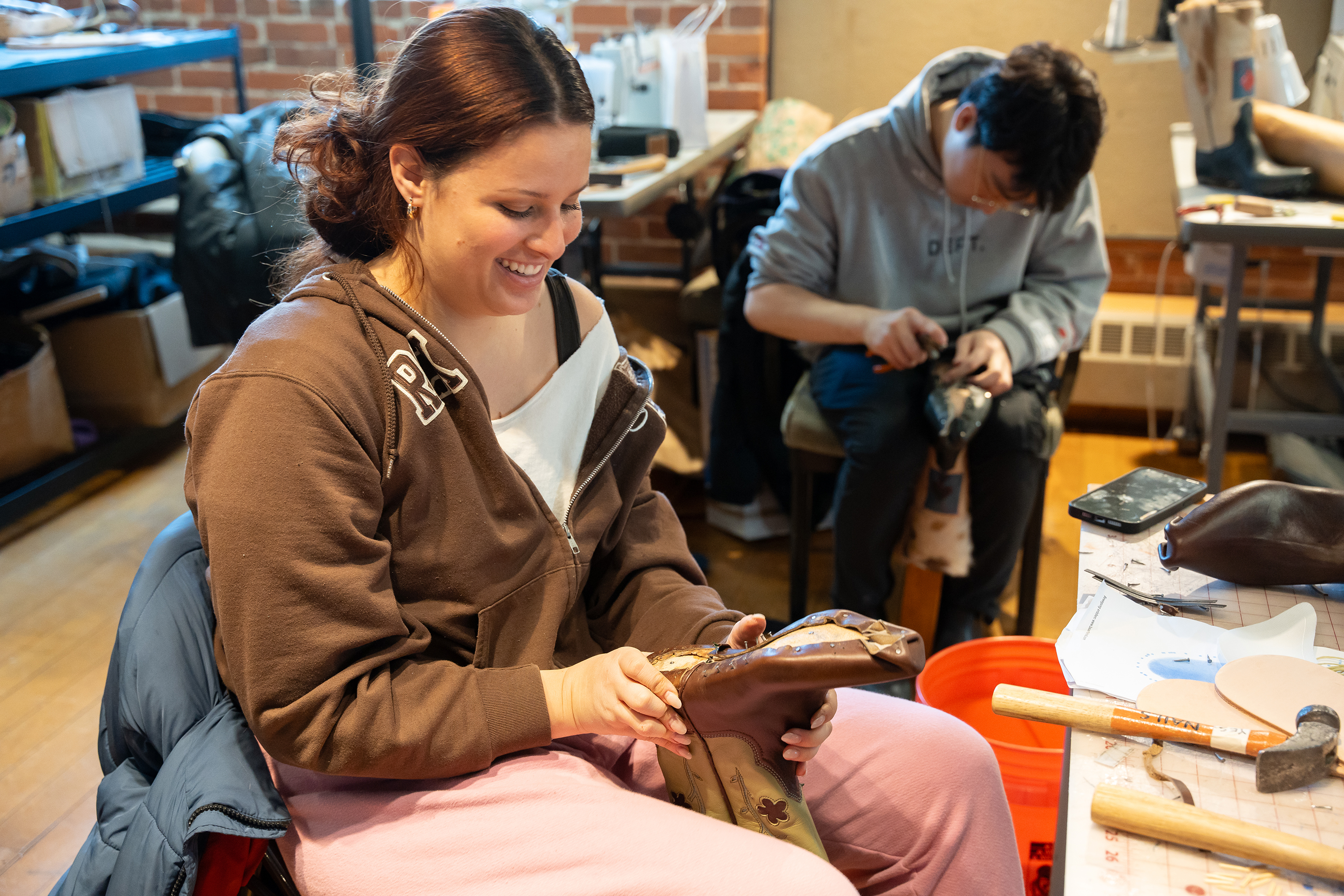
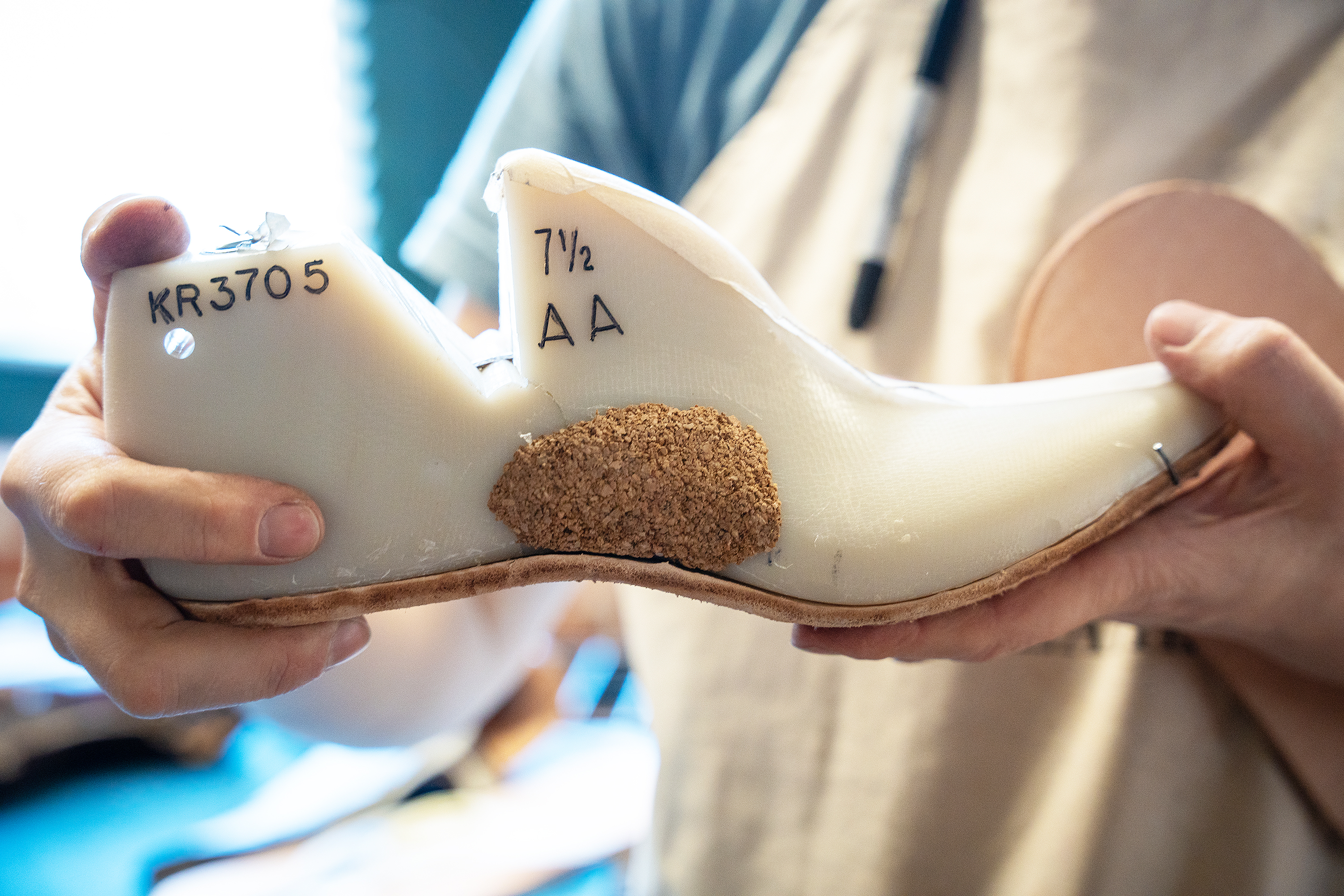
The original designs were partly based on vaquero-style boots worn by Mexican cowboys and featured tall tops, a pointed toe for easier entry into the stirrup and a sturdy stacked leather heel to keep the foot secure after mounting. Usually made from cowhide leather, contemporary cowboy boots feature all kinds of designs made from exotic materials derived from the ostrich, alligator, snake and buffalo.
“I wanted my design to be something earthy, and I was inspired by the iconic Luchese boot,” says Zsembery (pictured above). “I still need to do the stitching, but I’m terrified of the sewing machine!”
The students put down their tools and gather to watch Guerin demo the best method for attaching the vamp (or front part of the boot) to the last (the foot-shaped form that brings all of the boot’s parts together). “Cut two liners out of this super-soft orthopedic cowhide, which wicks moisture away from the foot,” she advises. She stretches the leather, which has been soaked in water, and uses pincers and clinching tacks to smooth away any wrinkles and hold the leather in place.
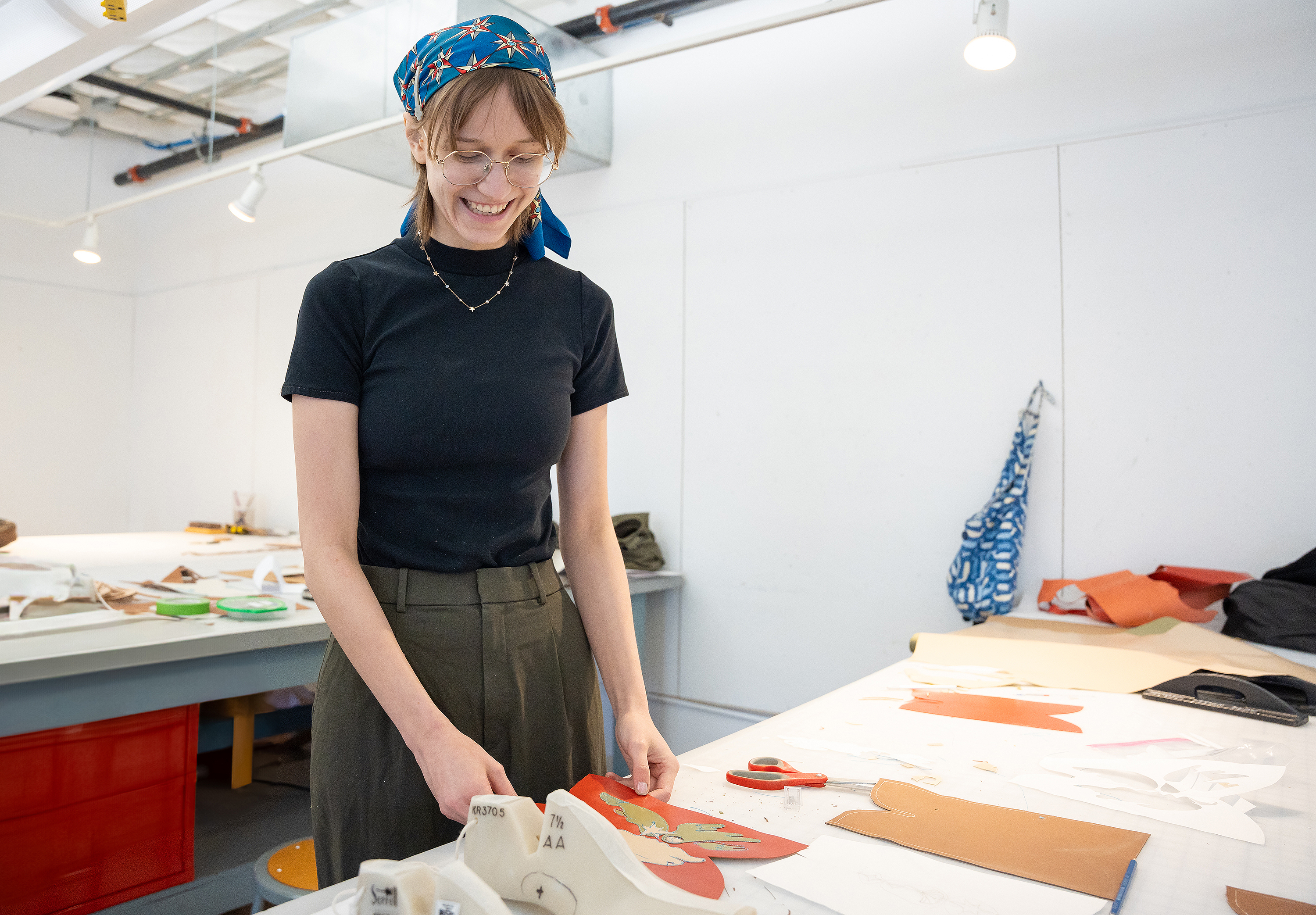
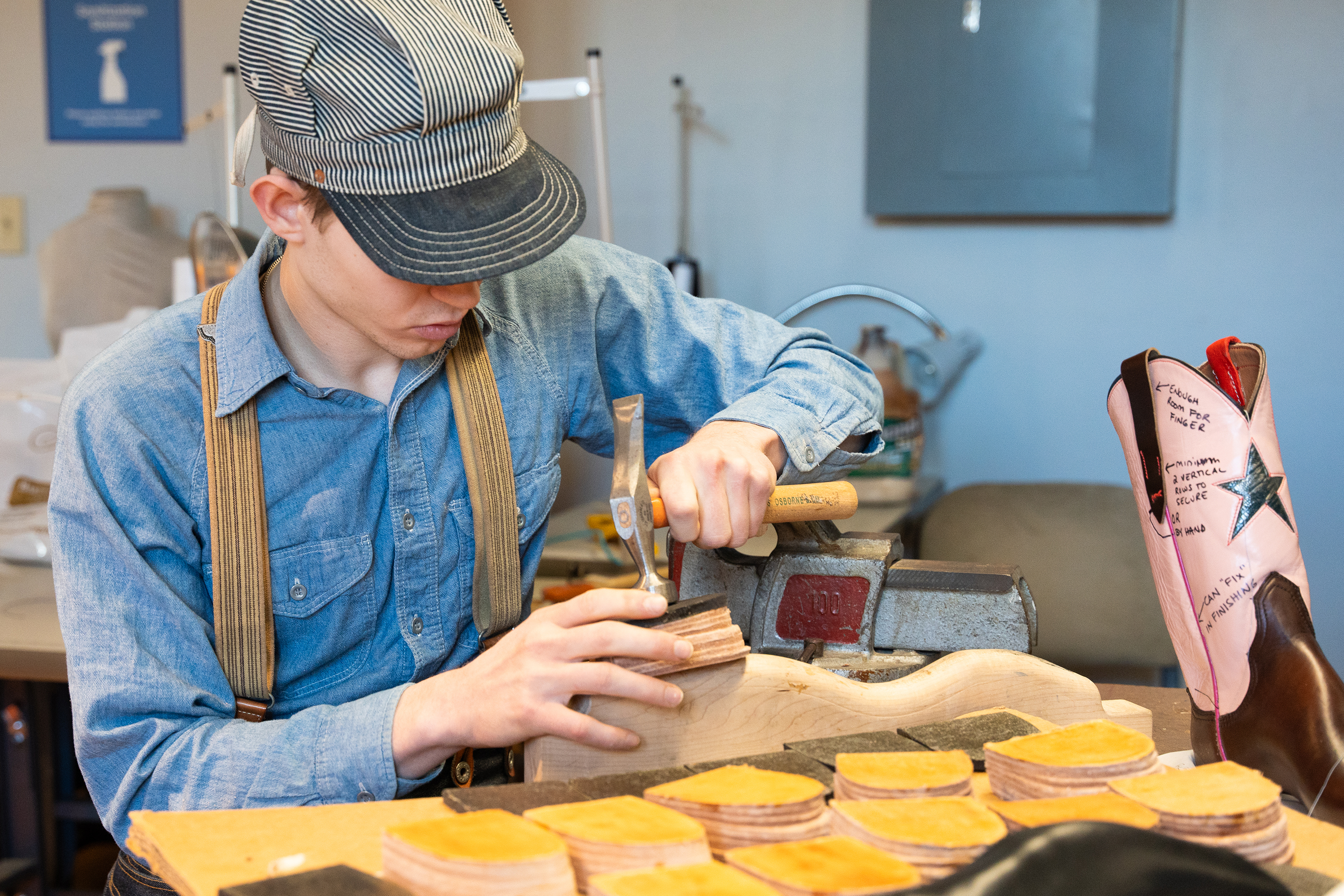
The boards the class is using are one-size and accommodate all boot sizes, but each student has also created pedographs (imprints of their footprints on paper) to ensure a perfect fit. “The process is hard on your hands,” Guerin notes. “If it starts to rip, stop tightening the screw, and if you get really frustrated, put it down and come back to it later.”
Over the course of five weeks, Guerin and class TA Milo Kolb 27 ID are supporting the students through every step of the complicated process: measuring their feet, adapting the boot lasts to fit their measurements, drafting, cutting and sewing the uppers, sanding down the premade heels using industrial sanders in the ID department and joining all the components together with the soles of the boots.
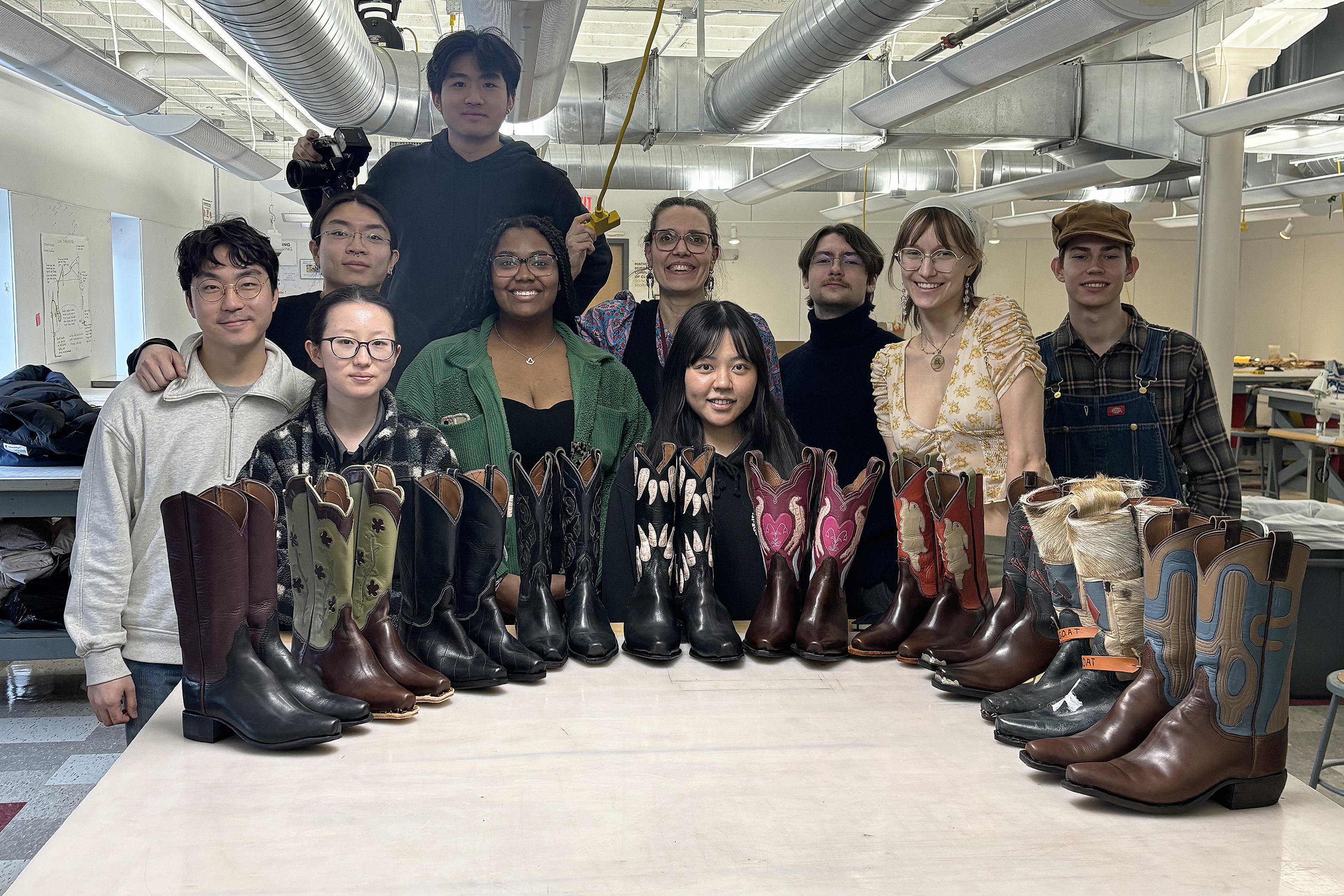
“The creative understanding that is required to turn flat templates into functional 3D footwear is critical to the curricula of both departments,” says Guerin. “In addition, these boots were designed to be repaired rather than being designed for obsolescence like so much modern factory-made footwear.”
Painting major Larisa Kachko 26 PT is working on a pair of red boots that will feature animal designs on the shafts. “I took an introductory shoemaking class last year,” she says, “and some of the techniques are the same. But last year, we glued the shoes together, and this time we’re sewing everything. I’m in love with my sewing machine!”
Simone Solondz / photos by Kaylee Pugliese
February 10, 2025